Modern CNC machining technologies have revolutionized the defense sector, enabling the production of components with unprecedented precision and repeatability. In this post, we’ll take a look at how advanced manufacturing processes affect the quality and reliability of military equipment, and the importance of this for national security. You’ll learn about key aspects of CNC machining in the context of the defense industry, and why precision manufacturing is so important in this sector.
What is CNC machining and what are its basic principles?
Machining is one of the most important manufacturing processes in industry, involving the removal of excess material from the workpiece in the form of chips. This precise process of shaping materials uses a variety of cutting tools that, through relative motion to the workpiece, gradually remove its outer layers, giving it the desired shape, dimensions and surface quality.
Key elements in CNC machining
There are several key elements in the CNC machining process. The first is the cutting tool, which can take a variety of forms – from simple turning knives to complex mills and drills. The second element is the workpiece, or material being machined. The third, equally important element, is the relative motion between the tool and the workpiece, which can be accomplished by rotary motion, reciprocating motion or a combination of these.
Modern machining uses advanced computer numerically controlled (CNC) machines to automate the entire process. Based on a numerical code, the CNC system controls all machining parameters: cutting speed, feed rate, depth of cut and tool movement trajectory. This makes it possible to achieve extremely high manufacturing precision, repeatability and process efficiency.
Depending on the type of machining, we can distinguish between several basic operations: turning (where the workpiece makes a rotary motion), milling (where the tool makes a rotary motion), drilling (used to make holes), grinding (using grinding wheels to achieve a high-quality surface) and other specialized methods. Each of these operations has its own specific applications and characteristics, and their appropriate selection depends on the requirements for the final product
What are the specifics of CNC machining in the defense industry?
The armaments sector places extremely high demands on manufacturing technologies. Military components must meet increased quality and durability standards. CNC machining for the armaments sector requires specialized machines and tools capable of guaranteeing the highest precision.
Maintaining tight control over the production process and documenting each machining step is also a key aspect. CNC systems allow full transparency and repeatability of the process, which is essential for the production of safety-critical components.
What materials are most commonly used in reinforcement manufacturing?
The reinforcement industry mainly uses materials with higher strength and resistance to extreme conditions. These include high-alloy steels, titanium alloys and high-tech composites. The processing of these materials requires specialized knowledge and experience.
The choice of the right material depends on the purpose of the component and the requirements for its mechanical and physical properties. Materials with enhanced corrosion and high temperature resistance are often used.
Why is precision crucial in military manufacturing?
Precision manufacturing in the arms sector can determine the lives of soldiers and the effectiveness of military operations. Even the slightest deviation from the intended parameters can affect the reliability of equipment in combat conditions.
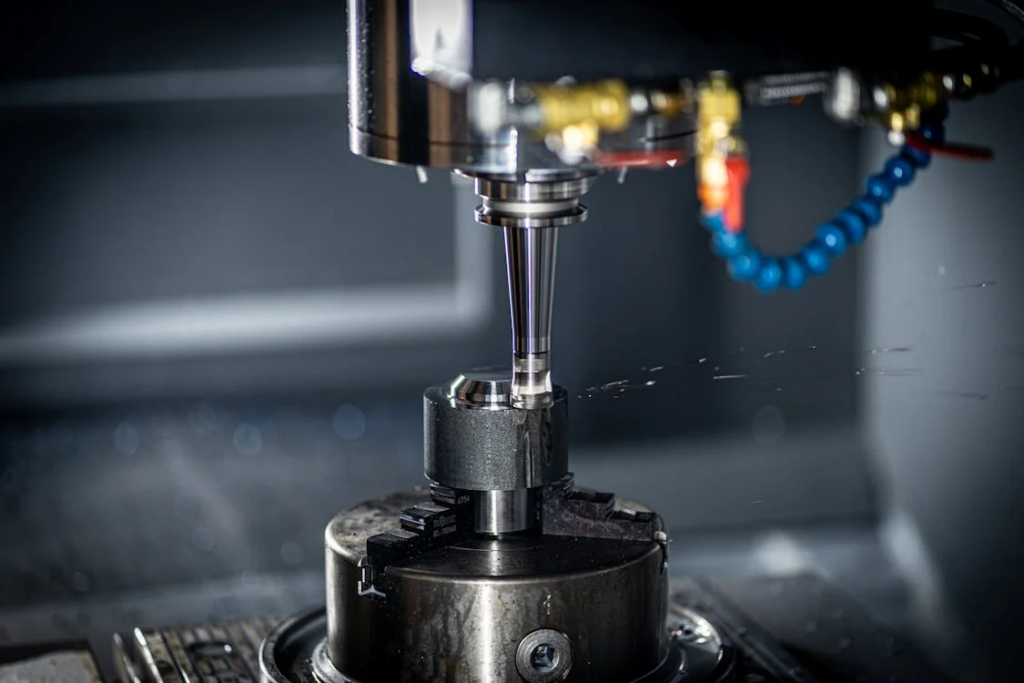
For weapons systems, where every millimeter counts, CNC technology makes it possible to achieve tolerances of micrometers. This is particularly important in the production of bearing components, trigger mechanisms or parts for guidance systems.
What are the latest trends in CNC technology for the defense industry?
Today’s trends in CNC machining for the military sector focus on automation and integration of production systems. Advanced real-time process monitoring and adaptive control systems are increasingly being used.
Technology developments are also leading to increased production efficiency while maintaining the highest quality standards. The implementation of artificial intelligence and machine learning allows optimization of processing parameters and anticipation of potential problems.
What does the quality control process look like in armament manufacturing?
The quality control system in the armament industry is multi-level and extremely rigorous. Each component is subject to detailed inspection using advanced measurement systems and non-destructive techniques.
The documentation of the manufacturing process must be complete and allow full traceability of each component. CNC systems automatically record machining parameters, which greatly facilitates the quality verification process.
Does production automation affect safety?
Automation of production processes in the defense sector affects safety in two ways. On the one hand, it increases the repeatability and precision of manufacturing, while on the other, it reduces the risk of human error.
Modern CNC machining centers are equipped with advanced safety systems that monitor the production process and automatically respond to any deviation from the set parameters.
What challenges do military component manufacturers face?
The main challenge is the need to constantly adapt to increasing technological and quality requirements. Manufacturers need to invest in the latest technologies and personnel training.
In addition, the defense sector requires the highest standards of information security and know-how protection. This requires the implementation of advanced security systems and access control procedures.
What will the future of CNC machining in the defense sector look like?
The future of CNC machining in the defense industry will most likely be associated with even greater automation and integration of production systems. The development of additive technologies may lead to hybrid solutions combining 3D printing with traditional machining.
Increased use of digital twin systems and simulation of manufacturing processes can also be expected, allowing processes to be optimized even before physical production begins.