Choosing the right materials for CNC machining is crucial to achieving high product quality and efficiency in the production process. In this article, we will discuss in detail how different materials affect CNC machining, their advantages and disadvantages, and how to select materials for your specific production needs. You will also learn which technical and practical aspects to consider when selecting materials in order to optimise the machining process.
How does material affect CNC machining performance?
Material selection has a key impact on the performance of CNC machining, which significantly affects production efficiency and the quality of the final products. The CNC machining process involves a variety of operations, such as milling, turning, drilling and tapping, which are sensitive to material properties. Each material has its own unique characteristics that can affect the efficiency of these operations.
What factors influence the CNC machining process?
The hardness of the material has a key impact on CNC machining. Hard materials, such as stainless steel or titanium, require stronger tools and adequate cooling to avoid overheating.
Material density also affects tool and machine load, which can lead to faster tool wear and higher production costs.
High thermal conductivity, as in the case of aluminium, facilitates heat dissipation, while materials with low conductivity may require better cooling.
The structure of the material, such as homogeneity or inclusions, also matters, influencing the choice of tools and machining techniques. By understanding these characteristics, the machining process can be optimised and the quality of the final products improved.
Metallic materials and CNC machining
Metallic materials are some of the most commonly machined materials in the CNC process. Here is some key information about this type of raw material to consider:
- Steel: this is a material of high hardness and strength. In CNC machining, it requires precision tools and adequate cooling to avoid overheating of the apparatus.
- Aluminium: is lighter and softer than steel, making it easier to machine. However, aluminium tends to stick to tools, which can lead to faster tool wear.
- Copper and brass: often used in the electronics industry, they have high electrical and thermal conductivity. Machining copper can be a challenge due to its softness and tendency to stick to tools.
Plastic materials in CNC machining
Plastics are widely used in many industries, from electronics to medicine. What is worth knowing about them?
POM (Polyoxymethylene, Polyacetal, Delrin)
- Properties: POM, also known as polyacetal or Delrin (trade name), is a thermoplastic polymer with high strength, stiffness and a low coefficient of friction. It is highly resistant to wear and has good mechanical properties, making it ideal for applications where precision and strength are required.
- Application: POM is often used in the manufacture of precision components such as bearings, gears, guide components, connectors and housings for electronic devices. Due to its abrasion resistance, it is often used in the automotive, engineering and white goods industries.
Teflon (PTFE – polytetrafluoroethylene)
- Properties: Teflon, also known as PTFE (polytetrafluoroethylene), is a plastic with an extremely low coefficient of friction, high resistance to temperatures (from -200°C to +260°C) and chemicals. It is also a non-stick material, which makes it widely used in the kitchen.
- Application: Teflon is most commonly known as a coating for frying pans and other kitchen utensils, which make it non-stick. In addition, it is also used in the chemical industry, where it is used for gaskets, sealants, cable insulation, as well as in the aerospace and medical industries.
Influence of material hardness on CNC machining
The hardness of a material is crucial to the machining process. Here is how it affects various aspects:
- Cutting tools: harder materials require more resistant tools, which can increase production costs.
- Machining parameters: harder materials often require lower cutting speeds and lower feed rates to ensure accuracy and avoid tool overheating.
- Tool life: harder materials wear out tools more quickly, which can lead to more frequent tool changes and increased running costs.
Choice of materials for specific applications
The choice of materials depends on the specific requirements of the project.
- Aerospace: often requires lightweight but robust materials such as titanium or aluminium alloys.
- Automotive: may require materials that can withstand high temperatures and pressures, such as metal alloys and chemical-resistant plastics.
- Electronics: requires materials with high electrical and thermal conductivity, such as copper and composite materials.
Tips for machining difficult materials
Machining difficult materials requires special attention. Read useful tips:
- Choosing the right tools: use tools that can withstand high temperatures and mechanical stress.
- Machine settings: adapt the machining parameters to the specific material, such as cutting speed and feed rate.
- Cooling: use the right coolants to prevent overheating of tools and material.
At Prasmet, you can count on help and support in selecting the right grade of material depending on the intended use of the manufactured element.
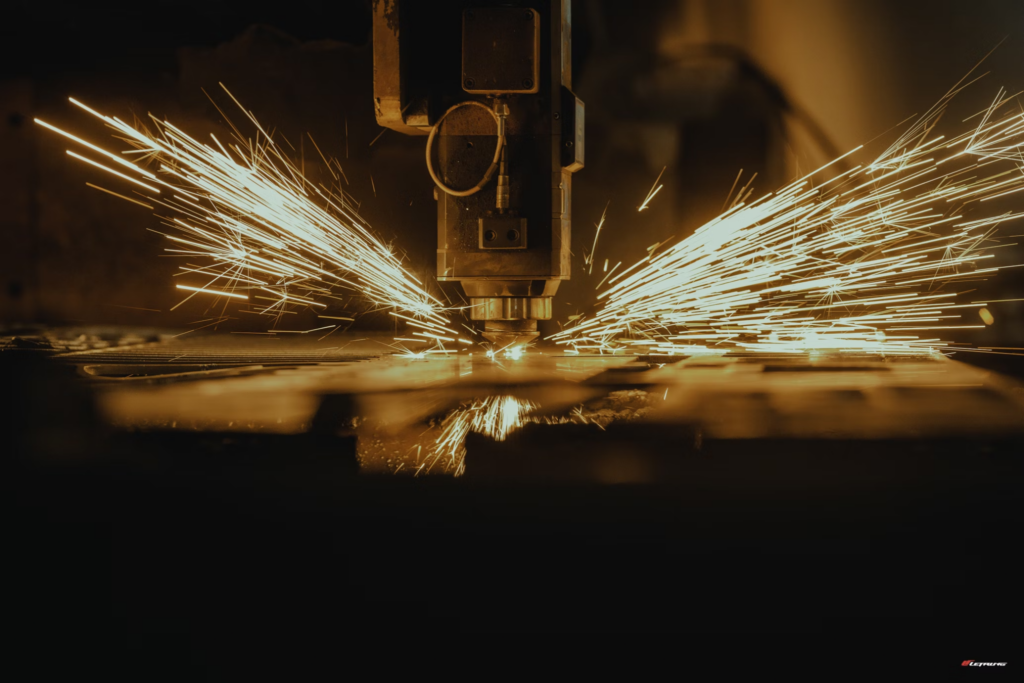