Przemysł motoryzacyjny wymaga najwyższej precyzji i niezawodności w produkcji różnorodnych części samochodowych. Ten kompleksowy przewodnik przedstawia kluczowe aspekty obróbki metali w kontekście motoryzacji, skupiając się na nowoczesnych technikach, bezpieczeństwie i efektywności. Poznaj najważniejsze metody obróbki mechanicznej, które rewolucjonizują produkcję nowoczesnych komponentów samochodowych.
Czym właściwie jest obróbka metali w przemyśle motoryzacyjnym?
Obróbka metali w przemyśle samochodowym to kompleksowy proces przekształcania surowych materiałów w precyzyjne komponenty. Jest to wieloetapowe przedsięwzięcie, rozpoczynające się od starannej selekcji materiałów wejściowych, takich jak stal nierdzewna, aluminium czy stopy specjalne. Każdy z tych materiałów wymaga indywidualnego podejścia i dostosowania parametrów obróbki do ich specyficznych właściwości mechanicznych. W procesie produkcji części samochodowych szczególną uwagę zwraca się na zachowanie odpowiedniej struktury krystalicznej metalu, która bezpośrednio wpływa na jego wytrzymałość i trwałość.
Wykorzystuje się do tego różnorodne techniki obróbki, od tradycyjnych metod mechanicznych po zaawansowane systemy CNC. Współczesne centra obróbcze pozwalają na wykonywanie złożonych operacji w jednym cyklu produkcyjnym, co znacząco skraca czas wytwarzania i zmniejsza ryzyko błędów. Tradycyjne metody, takie jak toczenie czy frezowanie, są nadal szeroko stosowane, ale zostały znacznie udoskonalone dzięki wprowadzeniu sterowania numerycznego i automatyzacji procesu.
W motoryzacji szczególnie ważne jest osiągnięcie wysokiej dokładności i powtarzalności wymiarów. Nowoczesne maszyny CNC potrafią pracować z dokładnością do kilku mikrometrów, co jest kluczowe przy produkcji elementów układów bezpieczeństwa, takich jak komponenty układów hamulcowych czy części silnika. Precyzja wykonania ma bezpośredni wpływ na żywotność części i ich niezawodne działanie w ekstremalnych warunkach.
Proces obróbki musi więc spełniać rygorystyczne normy jakościowe, gdyż od tego zależy bezpieczeństwo użytkowników pojazdów. Każdy etap produkcji podlega szczegółowej kontroli, wykorzystującej zaawansowane systemy pomiarowe i techniki badań nieniszczących.
Jakie znaczenie ma precyzja w produkcji części samochodowych?
Wysoka dokładność jest fundamentem bezpieczeństwa w motoryzacji. Współczesne pojazdy składają się z tysięcy precyzyjnie wykonanych elementów, które muszą ze sobą idealnie współpracować w różnych warunkach eksploatacji. Nawet minimalne odchylenia od założonych wymiarów mogą prowadzić do zwiększonego zużycia części, generowania nadmiernego hałasu czy – w skrajnych przypadkach – awarii krytycznych systemów bezpieczeństwa.
W przemyśle samochodowym wymagana jest wysoka dokładność przy wykonywaniu otworów o różnych wymiarach i kształtach. Dotyczy to szczególnie elementów układów mechanicznych, takich jak bloki silników, głowice czy elementy układów hamulcowych. Tolerancje wymiarowe w przypadku otworów montażowych czy prowadzących często nie przekraczają kilku mikrometrów, co wymaga stosowania specjalistycznych narzędzi i technik obróbki.
Jakie rodzaje obróbki mechanicznej są stosowane w przemyśle motoryzacyjnym?
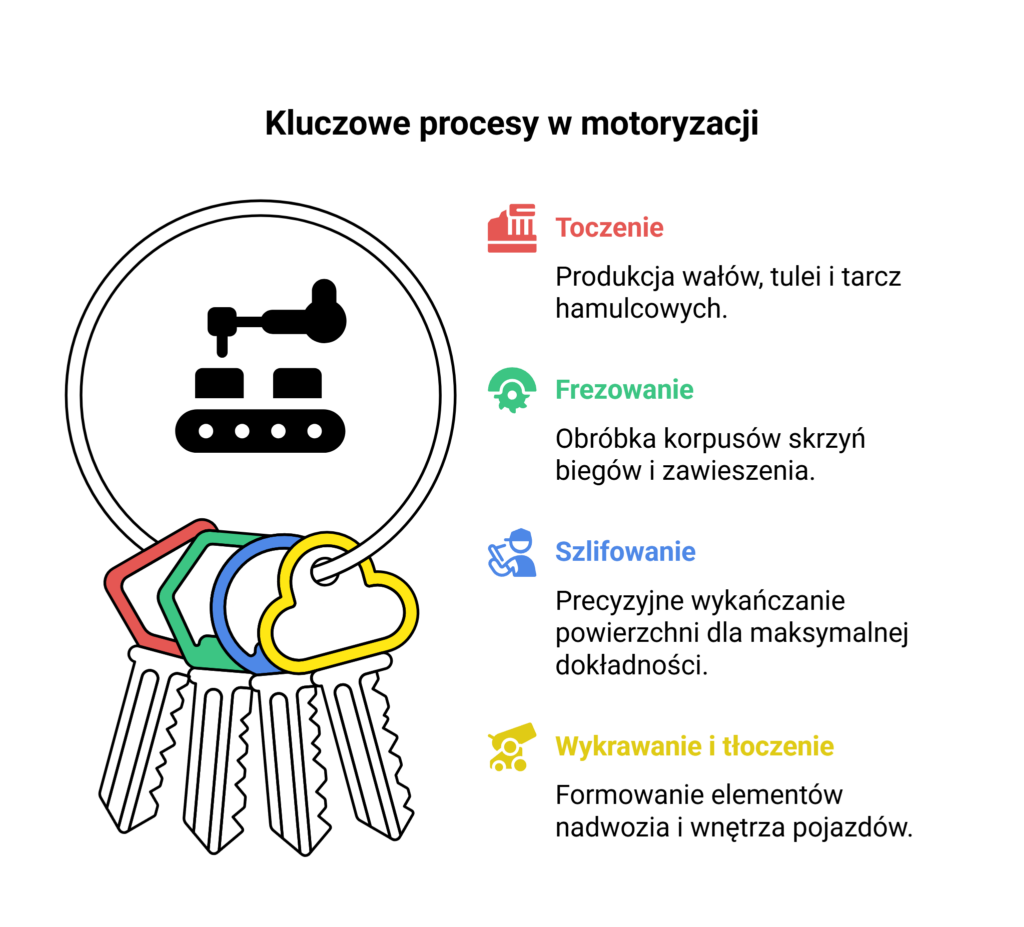
Podstawowymi metodami są toczenie, frezowanie i szlifowanie. Każda z tych metod ma swoje specyficzne zastosowanie w produkcji części samochodowych. Toczenie wykorzystywane jest głównie do wytwarzania elementów o przekroju kołowym, takich jak wały, tuleje czy tarcze hamulcowe. Frezowanie znajduje zastosowanie przy produkcji skomplikowanych kształtów, na przykład korpusów skrzyń biegów czy elementów zawieszenia. Szlifowanie jako proces wykończeniowy zapewnia najwyższą jakość powierzchni i precyzję wymiarową. Obróbka skrawaniem CNC z kolei pozwala na wykonywanie skomplikowanych elementów z najwyższą precyzją.
Maszyny sterowane numerycznie potrafią realizować złożone programy obróbcze, wykonując sekwencje różnych operacji bez konieczności przezbrajania. To znacząco zwiększa wydajność produkcji i gwarantuje powtarzalność wymiarową.
Dodatkowo wykorzystywane są prasy mechaniczne do wykrawania gięcia i tłoczenia elementów z metalowych blach. Procesy te są kluczowe przy produkcji zewnętrznych i wewnętrznych elementów pojazdu, gdzie liczy się nie tylko funkcjonalność, ale również estetyka wykonania. Nowoczesne prasy hydrauliczne i mimośrodowe wyposaża się w zaawansowane i precyzyjne przyrządy (takie jak wykrojniki, tłoczniki czy przyrządy wielozabiegowe), co pozwala na precyzyjne formowanie nawet bardzo skomplikowanych kształtów.
Co decyduje o wyborze metody obróbki metali?
Wybór odpowiedniej metody zależy od wielu czynników, m.in. od pożądanego kształtu, właściwości mechanicznych materiału i wymaganej twardości.
Forma obróbki musi być dostosowana do specyfiki produkcji różnych komponentów. Każda z tych metod ma swoje zalety i ograniczenia w zastosowaniu w przemyśle motoryzacyjnym.
Jak wygląda proces kontroli jakości w obróbce mechanicznej?
Kontrola jakości obejmuje pomiary wymiarów, badanie właściwości mechanicznych i testy wytrzymałościowe. Narzędzia pomiarowe są regularnie sprawdzane i kalibrowane.
Szczególną uwagę poświęca się sprawdzaniu dokładności wykonania i wykończenia powierzchni. Usługi obróbki CNC podlegają rygorystycznym procedurom kontrolnym.
W jaki sposób obróbka CNC zrewolucjonizowała produkcję części samochodowych?
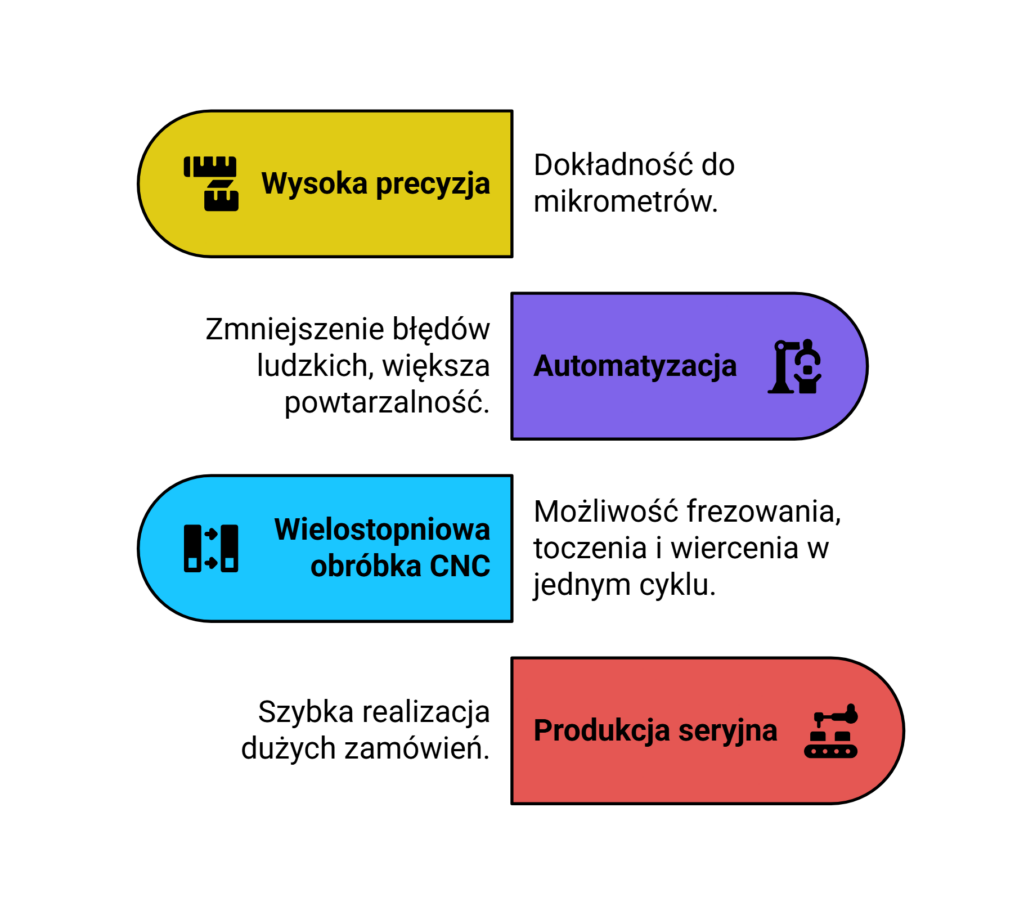
Computer Numerical Control (CNC) wprowadził nową jakość do przemysłu motoryzacyjnego. Maszyny CNC umożliwiają bowiem wykonywanie złożonych operacji z niespotykaną wcześniej dokładnością i powtarzalnością.
Obróbka CNC jest szczególnie ważna w przemyśle przy produkcji elementów takich jak bloki silników czy elementy układu hamulcowego. Narzędzie skrawające, sterowane komputerowo, wykonuje ruch z precyzją do mikrometrów.